Digital fabrication in architecture
The potential of digital tools is still unknown - How far can we go? - Will it constitute the conventional construction industry?

Architecture is all about designing and building. There has always been a dialogue between design development and realizing the project. With the development of CAD software, the newer generation of architects has many design processes to follow. These processes also influence the fabrication part of the project. Also, there are other perspectives such as, to reduce human labor, have more precision in manufacturing, faster production, and the ability to generate fluid forms the idea started to build with machines.
Before diving deep into the Subject of Digital fabrication; let’s take a look at the history of material manipulation. Humans have always designed a set of tools to accomplish the desired outcome. The inception was with Forming, applying mechanical pressure to shape the material to derive a new form. Cutting, removing material to form the new shape which also known as milling, sawing, and chiseling. Casting, an old technique to prepare hollow mold to get the desired shape. Joining, adding two or more forms of similar or different material together by welding, soldering, riveting, or bolting. And finally adding, a recent technique which uses deposition of material in successive layers. In digital fabrication, CAD refers to computer-aided design, and CAM refers to computer-aided modeling/manufacturing. Digital is a process, through which digital geometry design directly be produced through CNC (computer numerical control) machines.
Digital Fabrication has two aspects within: Physical to Digital and Digital to Physical. Physical to Digital refers to techniques used to transform a physical entity into a digital data format i.e., 3D scanning. Digital to Physical refers to techniques used to transform digital data format to physical entity i.e., subtractive, additive, and formative.

Figure 1 – Understanding Digital Fabrication. Source: author
Here we will talk about Digital to Physical.
- Subtractive fabrication – a technique by which 3D objects are constructed by successively cutting material away from a solid block of material. i.e., Laser cutter, Plasma cutter, Water jet cutter and CNC Milling router
- Additive fabrication – a technique by which 3D objects are constructed by adding layer upon layer of material. i.e., 3d printer
- Formative fabrication – a process by which 3D objects are constructed by applying mechanical forces to reform or reshape the material. i.e., robotic manipulation
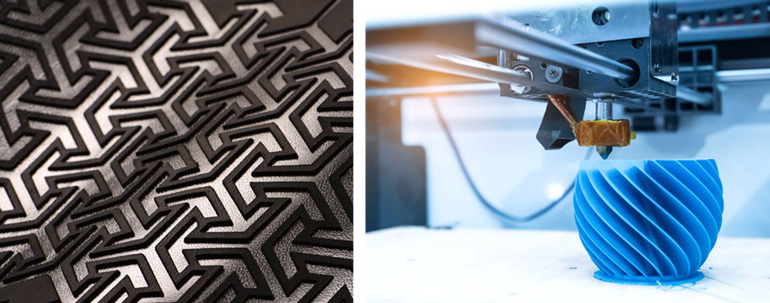
Machines cannot understand the CAD data so it has to be translated into CAM data which is a code understood by it. In CNC operations the CAM data is known as G-Code, a simple code generated by series of coordinates.
Let’s discuss each technique and their tools in detail and their advantages.
Subtractive Fabrication
Laser cutter, one of the most common and accessible form of digital fabrication. It is a popular tool among architectural / design schools, professional model makers as well as industry. They are mostly suitable for cutting materials which are less than 20 mm.
The advantage of laser cutting is high degree of accuracy, precision and clean cut. The material range includes, paper, plastic, different kind of boards, wood, metal and even textiles. There are majorly three types of laser cutters, CO2 laser cutter, Crystal laser cutter and Fiber laser cutter.
CNC (computer numerically controlled) milling router, Routing (2 axis) and Milling (3 and more axis) operations by which solid mass has been removed from the material to get the desired form. The major differences between a CNC milling router and Laser cutter are:
- Laser cutters can move into two axis, X and Y while CNC milling routers have four – six even eight axis.
- CNC milling routers can perform operations on variety of materials as well as larger depths up to 100 mm and more.
Additive Fabrication
Fused Deposition Modelling (FDM), The most general 3D printing technology; here the 3d Printers uses thermoplastic material (filament) which melts and deposited in successive layers to create desired element. The known thermoplastic filaments are ABS, PLA, PVA etc. FDM technology is vastly used in architectural schools and in model making.
Stereolithography (SLA), here the 3D printer uses a laser to cure liquid resin into hardened plastic. The advantages of using SLA are highly accurate, smooth finished and fine detailed objects.
Selective laser sintering (SLS), here the 3D printer uses a high-powered laser to fuse the polyamide powder to create desired element. 3d elements printed from SLS technology has higher mechanical strength.
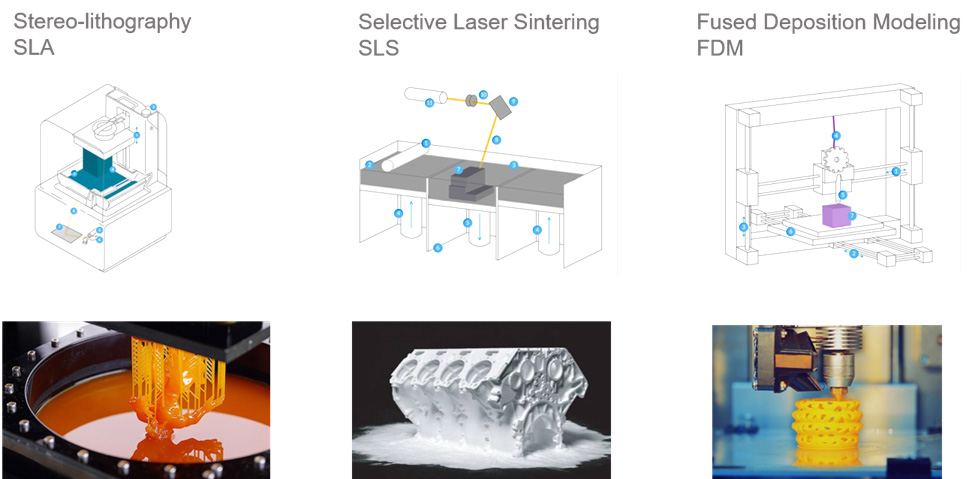
Why do we need digital fabrication?
We understand that the outcome is more precise when built with digital tools but they also require certain post processing and there is a long list of logistics and maintenance which needs to be followed while using every machine. However, considering today’s scenario where everything we design are in digital format, it makes sense to transfer the digital data to machines to construct the project.

In the future of digital building in architecture, digital tools give the advantage to build fluid forms. But are they sustainable? In the current scenario, the educational institutes such as ETH Zurich, UCL – Bartlett, AA – London, ICD – Germany, etc. are experimenting highly with digital tools but apart from educational institutes, there are not many practices that are using digital tools in the routine. The main reason is structures built from these tools are special structures and they cannot suddenly replace the conventional way of building.

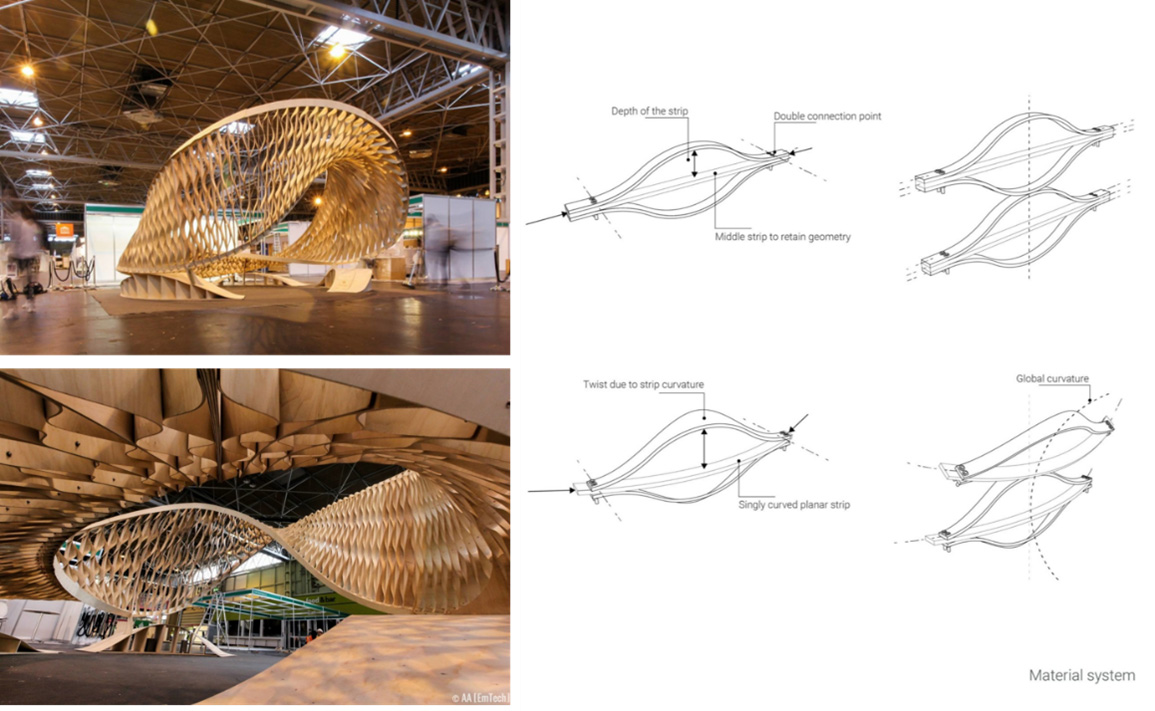
We are moving towards a digital age, where we want to build with precision and in mass so that’s where these digital tools are headed. We are seeing the examples of using a 3D printer to construct houses, where the filament is replaced by concrete and it can produce in weeks if not days! Robotic arms such as Kuka where the head of it can be replaced by a laser cutting nozzle, 3d printing extruder, or a CNC milling router; can perform a variety of operations within one.
Part of digital tools, such as 3D scanning has been vastly used by architects and designers in mapping. It opens a new door to redesign and relearn. One of the exquisite examples of it is, Sagrada di Familia reconstruction; whereas digital tools have been used vastly to recreate the elements and scale them up to the project scale.
The potential of digital tools still is unknown and how far we will go, will it replace partially or totally the conventional building industry? It has already replaced the design development so will it affect the overall architecture industry? These are the questions which we have to look forward to in the future.